Positive displacement pumps
Introduction
A positive displacement pump is one in which a definite volume of liquid is delivered for each cycle of pump operation. This volume is constant regardless of the resistance to flow offered by the system the pump is in, provided the capacity of the power unit driving the pump or pump component strength limits are not exceeded. The positive displacement pump delivers liquid in separate volumes with no delivery in between, although a pump having several chambers may have an overlapping delivery among individual chambers, which minimizes this effect. The positive displacement pump differs from centrifugal pumps, which deliver a continuous flow for any given pump speed and discharge resistance.
Positive displacement pumps can be grouped into three basic categories based on their design and operation. The three groups are reciprocating pumps, rotary pumps, and diaphragm pumps.
Principle of Operation
All positive displacement pumps operate on the same basic principle. This principle can be most easily demonstrated by considering a reciprocating positive displacement pump consisting of a single reciprocating piston in a cylinder with a single suction port and a single discharge port as shown in Figure 12. Check valves in the suction and discharge ports allow flow in only one direction.
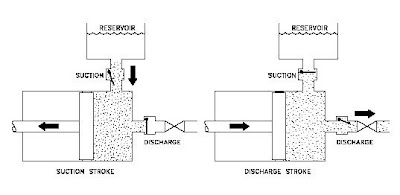
Figure 12 Reciprocating Positive Displacement Pump Operation
A positive displacement pump is one in which a definite volume of liquid is delivered for each cycle of pump operation. This volume is constant regardless of the resistance to flow offered by the system the pump is in, provided the capacity of the power unit driving the pump or pump component strength limits are not exceeded. The positive displacement pump delivers liquid in separate volumes with no delivery in between, although a pump having several chambers may have an overlapping delivery among individual chambers, which minimizes this effect. The positive displacement pump differs from centrifugal pumps, which deliver a continuous flow for any given pump speed and discharge resistance.
Positive displacement pumps can be grouped into three basic categories based on their design and operation. The three groups are reciprocating pumps, rotary pumps, and diaphragm pumps.
Principle of Operation
All positive displacement pumps operate on the same basic principle. This principle can be most easily demonstrated by considering a reciprocating positive displacement pump consisting of a single reciprocating piston in a cylinder with a single suction port and a single discharge port as shown in Figure 12. Check valves in the suction and discharge ports allow flow in only one direction.
Figure 12 Reciprocating Positive Displacement Pump Operation
During the suction stroke, the piston moves to the left, causing the check valve in the suction line between the reservoir and the pump cylinder to open and admit water from the reservoir.
During the discharge stroke, the piston moves to the right, seating the check valve in the suction line and opening the check valve in the discharge line. The volume of liquid moved by the pump in one cycle (one suction stroke and one discharge stroke) is equal to the change in the liquid volume of the cylinder as the piston moves from its farthest left position to its farthest right position.
Reciprocating Pumps
Reciprocating positive displacement pumps are generally categorized in four ways: direct-acting or indirect-acting; simplex or duplex; single-acting or double-acting; and power pump
Direct-Acting and Indirect-Acting Pumps
Some reciprocating pumps are powered by prime movers that also have reciprocating
motion, such as a reciprocating pump powered by a reciprocating steam piston. The piston rod of the steam piston may be directly connected to the liquid piston of the pump or it may be indirectly connected with a beam or linkage. Direct-acting pumps have a plunger on the liquid (pump) end that is directly driven by the pump rod (also the piston rod or extension thereof) and carries the piston of the power end. Indirect-acting pumps are driven by means of a beam or linkage connected to and actuated by the power piston rod of a separate reciprocating engine.
Simplex and Duplex Pumps
A simplex pump, sometimes referred to as a single pump, is a pump having a single liquid (pump) cylinder. A duplex pump is the equivalent of two simplex pumps placed side by side on the same foundation.
The driving of the pistons of a duplex pump is arranged in such a manner that when one piston is on its upstroke the other piston is on its downstroke, and vice versa. This arrangement doubles the capacity of the duplex pump compared to a simplex pump of comparable design.
Single-Acting and Double-Acting Pumps
A single-acting pump is one that takes a suction, filling the pump cylinder on the stroke in only one direction, called the suction stroke, and then forces the liquid out of the cylinder on the return stroke, called the discharge stroke. A double-acting pump is one that, as it fills one end of the liquid cylinder, is discharging liquid from the other end of the cylinder.
On the return stroke, the end of the cylinder just emptied is filled, and the end just filled is emptied. One possible arrangement for single-acting and double-acting pumps is shown in Figure 13.
Power Pumps
Power pumps convert rotary motion to low speed reciprocating motion by reduction
gearing, a crankshaft, connecting rods and crossheads. Plungers or pistons are driven by the crosshead drives. Rod and piston construction, similar to duplex double-acting steam pumps, is used by the liquid ends of the low pressure, higher capacity units. The higher pressure units are normally single-acting plungers, and usually employ three (triplex) plungers. Three or more plungers substantially reduce flow pulsations relative to simplex and even duplex pumps.

Figure 13 Single-Acting and Double-Acting Pumps
During the discharge stroke, the piston moves to the right, seating the check valve in the suction line and opening the check valve in the discharge line. The volume of liquid moved by the pump in one cycle (one suction stroke and one discharge stroke) is equal to the change in the liquid volume of the cylinder as the piston moves from its farthest left position to its farthest right position.
Reciprocating Pumps
Reciprocating positive displacement pumps are generally categorized in four ways: direct-acting or indirect-acting; simplex or duplex; single-acting or double-acting; and power pump
Direct-Acting and Indirect-Acting Pumps
Some reciprocating pumps are powered by prime movers that also have reciprocating
motion, such as a reciprocating pump powered by a reciprocating steam piston. The piston rod of the steam piston may be directly connected to the liquid piston of the pump or it may be indirectly connected with a beam or linkage. Direct-acting pumps have a plunger on the liquid (pump) end that is directly driven by the pump rod (also the piston rod or extension thereof) and carries the piston of the power end. Indirect-acting pumps are driven by means of a beam or linkage connected to and actuated by the power piston rod of a separate reciprocating engine.
Simplex and Duplex Pumps
A simplex pump, sometimes referred to as a single pump, is a pump having a single liquid (pump) cylinder. A duplex pump is the equivalent of two simplex pumps placed side by side on the same foundation.
The driving of the pistons of a duplex pump is arranged in such a manner that when one piston is on its upstroke the other piston is on its downstroke, and vice versa. This arrangement doubles the capacity of the duplex pump compared to a simplex pump of comparable design.
Single-Acting and Double-Acting Pumps
A single-acting pump is one that takes a suction, filling the pump cylinder on the stroke in only one direction, called the suction stroke, and then forces the liquid out of the cylinder on the return stroke, called the discharge stroke. A double-acting pump is one that, as it fills one end of the liquid cylinder, is discharging liquid from the other end of the cylinder.
On the return stroke, the end of the cylinder just emptied is filled, and the end just filled is emptied. One possible arrangement for single-acting and double-acting pumps is shown in Figure 13.
Power Pumps
Power pumps convert rotary motion to low speed reciprocating motion by reduction
gearing, a crankshaft, connecting rods and crossheads. Plungers or pistons are driven by the crosshead drives. Rod and piston construction, similar to duplex double-acting steam pumps, is used by the liquid ends of the low pressure, higher capacity units. The higher pressure units are normally single-acting plungers, and usually employ three (triplex) plungers. Three or more plungers substantially reduce flow pulsations relative to simplex and even duplex pumps.
Figure 13 Single-Acting and Double-Acting Pumps
Power pumps typically have high efficiency and are capable of developing very high pressures.
They can be driven by either electric motors or turbines. They are relatively expensive pumps and can rarely be justified on the basis of efficiency over centrifugal pumps. However, they are frequently justified over steam reciprocating pumps where continuous duty service is needed due to the high steam requirements of direct-acting steam pumps.
In general, the effective flow rate of reciprocating pumps decreases as the viscosity of the fluid being pumped increases because the speed of the pump must be reduced. In contrast to centrifugal pumps, the differential pressure generated by reciprocating pumps is independent of fluid density. It is dependent entirely on the amount of force exerted on the piston. For more information on viscosity, density, and positive displacement pump theory, refer to the handbook on Thermodynamics, Heat Transfer, and Fluid Flow.
Rotary Pumps
Rotary pumps operate on the principle that a rotating vane, screw, or gear traps the liquid in the suction side of the pump casing and forces it to the discharge side of the casing. These pumps are essentially self-priming due to their capability of removing air from suction lines and producing a high suction lift. In pumps designed for systems requiring high suction lift and self priming features, it is essential that all clearances between rotating parts, and between rotating and stationary parts, be kept to a minimum in order to reduce slippage. Slippage is leakage of fluid from the discharge of the pump back to its suction.
Due to the close clearances in rotary pumps, it is necessary to operate these pumps at relatively low speed in order to secure reliable operation and maintain pump capacity over an extended period of time. Otherwise, the erosive action due to the high velocities of the liquid passing through the narrow clearance spaces would soon cause excessive wear and increased clearances, resulting in slippage.
There are many types of positive displacement rotary pumps, and they are normally grouped into three basic categories that include gear pumps, screw pumps, and moving vane pumps.
Simple Gear Pump
There are several variations of gear pumps. The simple gear pump shown in Figure 14 consists of two spur gears meshing together and revolving in opposite directions within a casing. Only a few thousandths of an inch clearance exists between the case and the gear faces and teeth extremities. Any liquid that fills the space bounded by two successive gear teeth and the case must follow along with the teeth as they revolve. When the gear teeth mesh with the teeth of the other gear, the space between the teeth is reduced, and the entrapped liquid is forced out the pump discharge pipe.
As the gears revolve and the teeth disengage, the space again opens on the suction side of the pump, trapping new quantities of liquid and carrying it around the pump case to the discharge. As liquid is carried away from the suction side, a lower pressure is created, which draws liquid in through the suction line.

Fig 24 Simple Gear Pump
They can be driven by either electric motors or turbines. They are relatively expensive pumps and can rarely be justified on the basis of efficiency over centrifugal pumps. However, they are frequently justified over steam reciprocating pumps where continuous duty service is needed due to the high steam requirements of direct-acting steam pumps.
In general, the effective flow rate of reciprocating pumps decreases as the viscosity of the fluid being pumped increases because the speed of the pump must be reduced. In contrast to centrifugal pumps, the differential pressure generated by reciprocating pumps is independent of fluid density. It is dependent entirely on the amount of force exerted on the piston. For more information on viscosity, density, and positive displacement pump theory, refer to the handbook on Thermodynamics, Heat Transfer, and Fluid Flow.
Rotary Pumps
Rotary pumps operate on the principle that a rotating vane, screw, or gear traps the liquid in the suction side of the pump casing and forces it to the discharge side of the casing. These pumps are essentially self-priming due to their capability of removing air from suction lines and producing a high suction lift. In pumps designed for systems requiring high suction lift and self priming features, it is essential that all clearances between rotating parts, and between rotating and stationary parts, be kept to a minimum in order to reduce slippage. Slippage is leakage of fluid from the discharge of the pump back to its suction.
Due to the close clearances in rotary pumps, it is necessary to operate these pumps at relatively low speed in order to secure reliable operation and maintain pump capacity over an extended period of time. Otherwise, the erosive action due to the high velocities of the liquid passing through the narrow clearance spaces would soon cause excessive wear and increased clearances, resulting in slippage.
There are many types of positive displacement rotary pumps, and they are normally grouped into three basic categories that include gear pumps, screw pumps, and moving vane pumps.
Simple Gear Pump
There are several variations of gear pumps. The simple gear pump shown in Figure 14 consists of two spur gears meshing together and revolving in opposite directions within a casing. Only a few thousandths of an inch clearance exists between the case and the gear faces and teeth extremities. Any liquid that fills the space bounded by two successive gear teeth and the case must follow along with the teeth as they revolve. When the gear teeth mesh with the teeth of the other gear, the space between the teeth is reduced, and the entrapped liquid is forced out the pump discharge pipe.
As the gears revolve and the teeth disengage, the space again opens on the suction side of the pump, trapping new quantities of liquid and carrying it around the pump case to the discharge. As liquid is carried away from the suction side, a lower pressure is created, which draws liquid in through the suction line.
Fig 24 Simple Gear Pump
With the large number of teeth usually employed on the gears, the discharge is relatively smooth and continuous, with small quantities of liquid being delivered to the discharge line in rapid succession. If designed with fewer teeth, the space between the teeth is greater and the capacity increases for a given speed; however, the tendency toward a pulsating discharge increases. In all simple gear pumps, power is applied to the shaft of one of the gears, which transmits power to the driven gear through their meshing teeth.
There are no valves in the gear pump to cause friction losses as in the reciprocating pump.
The high impeller velocities, with resultant friction losses, are not required as in the
centrifugal pump. Therefore, the gear pump is well suited for handling viscous fluids such as fuel and lubricating oils.
Other Gear Pumps
There are two types of gears used in gear pumps in addition to the simple spur gear. One type is the helical gear. A helix is the curve produced when a straight line moves up or down the surface of a cylinder. The other type is the herringbone gear. A herringbone gear is composed of two helixes spiraling in different directions from the center of the gear. Spur, helical, and herringbone gears are shown in Figure 15.
The helical gear pump has advantages over the simple spur gear. In a spur gear, the entire length of the gear tooth engages at the same time. In a helical gear, the point of engagement moves along the length of the gear tooth as the gear rotates. This makes the helical gear operate with a steadier discharge pressure and fewer pulsations than a spur gear pump.
The herringbone gear pump is also a modification of the simple gear pump. Its principal difference in operation from the simple spur gear pump is that the pointed center section of the space between two teeth begins discharging before the divergent outer ends of the preceding space complete discharging. This
overlapping tends to provide a steadier discharge pressure. The power transmission from the driving to the driven gear is also smoother and
quieter.
Lobe Type Pump
The lobe type pump shown in Figure 16 is another variation of the simple gear pump. It is considered as a simple gear pump having only two or three teeth per rotor; otherwise, its operation or the
explanation of the function of its parts is no different. Some designs of lobe pumps are fitted with replaceable gibs, that is, thin plates carried in grooves at the extremity of each lobe where they
make contact with the casing. The gib promotes tightness and absorbs radial wear.
Screw-Type Positive Displacement Rotary Pump
There are many variations in the design of the screw type positive displacement, rotary pump. The primary differences consist of the number of intermeshing screws involved, the pitch of the screws, and the general direction of fluid flow. Two common designs are the two-screw, low-pitch, double-flow pump and the three-screw, high-pitch, double-flow pump.
*Two-Screw, Low-Pitch, Screw Pump
The two-screw, low-pitch, screw pump consists of two screws that mesh with close
clearances, mounted on two parallel shafts. One screw has a right-handed thread, and
the other screw has a left-handed thread. One shaft is the driving shaft and drives the
other shaft through a set of herringbone timing gears. The gears serve to maintain
clearances between the screws as they turn and to promote quiet operation. The
screws rotate in closely fitting duplex cylinders that have overlapping bores. All
clearances are small, but there is no actual contact between the two screws or between
the screws and the cylinder walls.
The complete assembly and the usual flow Figure 18 Three-Screw, High-Pitch, Screw Pump path are shown in Figure 17. Liquid is trapped at the outer end of each pair of screws. As the first space between the screw threads rotates away from the opposite screw, a one-turn, spiral-shaped quantity of liquid is enclosed when the end of the screw again meshes with the opposite screw. As the
screw continues to rotate, the entrapped spiral turns of liquid slide along the cylinder toward the center discharge space while the next slug is being entrapped.
Each screw functions similarly, and each pair of screws discharges an equal quantity of liquid in opposed streams toward the center, thus eliminating hydraulic thrust. The removal of liquid from the suction end by the screws produces a
reduction in pressure, which draws liquid through the suction line.
*Three-Screw, High-Pitch, Screw Pump
The three-screw, high-pitch, screw pump, shown in Figure 18, has many of the same elements as the two-screw, low-pitch, screw pump, and their operations are similar.
Three screws, oppositely threaded on each end, are employed. They rotate in a triple cylinder, the two outer bores of which overlap the center bore. The pitch of the screws is much higher than in the low pitch screw pump; therefore, the center screw, or
power rotor, is used to drive the two outer idler rotors directly without external timing gears.
Pedestal bearings at the base support the weight of the rotors and maintain their axial position. The liquid being pumped enters the suction opening, flows through passages around the rotor housing, and through the screws from each end, in opposed
streams, toward the center discharge. This eliminates unbalanced hydraulic thrust.
The screw pump is used for pumping viscous fluids, usually lubricating, hydraulic, or fuel oil.
Rotary Moving Vane Pump
The rotary moving vane pump shown in Figure 19 is another type of positive displacement pump used. The pump consists of a cylindrically bored housing with a suction inlet on one side and a discharge outlet on the other. A cylindrically shaped rotor with a diameter smaller than the cylinder is driven about an axis placed above the centerline of the cylinder.
The clearance between rotor and cylinder is small at the top but increases at the bottom.
The rotor carries vanes that move in and out as it rotates to maintain sealed spaces between the rotor and the cylinder wall. The vanes trap liquid or gas on the suction side and carry it to the discharge side, where contraction of the space expels it through the discharge line.The vanes may swing on pivots, or they may slide in slots in the rotor.

There are no valves in the gear pump to cause friction losses as in the reciprocating pump.
The high impeller velocities, with resultant friction losses, are not required as in the
centrifugal pump. Therefore, the gear pump is well suited for handling viscous fluids such as fuel and lubricating oils.
Other Gear Pumps
There are two types of gears used in gear pumps in addition to the simple spur gear. One type is the helical gear. A helix is the curve produced when a straight line moves up or down the surface of a cylinder. The other type is the herringbone gear. A herringbone gear is composed of two helixes spiraling in different directions from the center of the gear. Spur, helical, and herringbone gears are shown in Figure 15.
The helical gear pump has advantages over the simple spur gear. In a spur gear, the entire length of the gear tooth engages at the same time. In a helical gear, the point of engagement moves along the length of the gear tooth as the gear rotates. This makes the helical gear operate with a steadier discharge pressure and fewer pulsations than a spur gear pump.
The herringbone gear pump is also a modification of the simple gear pump. Its principal difference in operation from the simple spur gear pump is that the pointed center section of the space between two teeth begins discharging before the divergent outer ends of the preceding space complete discharging. This
overlapping tends to provide a steadier discharge pressure. The power transmission from the driving to the driven gear is also smoother and
quieter.
Lobe Type Pump
The lobe type pump shown in Figure 16 is another variation of the simple gear pump. It is considered as a simple gear pump having only two or three teeth per rotor; otherwise, its operation or the
explanation of the function of its parts is no different. Some designs of lobe pumps are fitted with replaceable gibs, that is, thin plates carried in grooves at the extremity of each lobe where they
make contact with the casing. The gib promotes tightness and absorbs radial wear.
Screw-Type Positive Displacement Rotary Pump
There are many variations in the design of the screw type positive displacement, rotary pump. The primary differences consist of the number of intermeshing screws involved, the pitch of the screws, and the general direction of fluid flow. Two common designs are the two-screw, low-pitch, double-flow pump and the three-screw, high-pitch, double-flow pump.
*Two-Screw, Low-Pitch, Screw Pump
The two-screw, low-pitch, screw pump consists of two screws that mesh with close
clearances, mounted on two parallel shafts. One screw has a right-handed thread, and
the other screw has a left-handed thread. One shaft is the driving shaft and drives the
other shaft through a set of herringbone timing gears. The gears serve to maintain
clearances between the screws as they turn and to promote quiet operation. The
screws rotate in closely fitting duplex cylinders that have overlapping bores. All
clearances are small, but there is no actual contact between the two screws or between
the screws and the cylinder walls.
screw continues to rotate, the entrapped spiral turns of liquid slide along the cylinder toward the center discharge space while the next slug is being entrapped.
Each screw functions similarly, and each pair of screws discharges an equal quantity of liquid in opposed streams toward the center, thus eliminating hydraulic thrust. The removal of liquid from the suction end by the screws produces a
reduction in pressure, which draws liquid through the suction line.
The three-screw, high-pitch, screw pump, shown in Figure 18, has many of the same elements as the two-screw, low-pitch, screw pump, and their operations are similar.
Three screws, oppositely threaded on each end, are employed. They rotate in a triple cylinder, the two outer bores of which overlap the center bore. The pitch of the screws is much higher than in the low pitch screw pump; therefore, the center screw, or
power rotor, is used to drive the two outer idler rotors directly without external timing gears.
Pedestal bearings at the base support the weight of the rotors and maintain their axial position. The liquid being pumped enters the suction opening, flows through passages around the rotor housing, and through the screws from each end, in opposed
streams, toward the center discharge. This eliminates unbalanced hydraulic thrust.
The screw pump is used for pumping viscous fluids, usually lubricating, hydraulic, or fuel oil.
Rotary Moving Vane Pump
The rotary moving vane pump shown in Figure 19 is another type of positive displacement pump used. The pump consists of a cylindrically bored housing with a suction inlet on one side and a discharge outlet on the other. A cylindrically shaped rotor with a diameter smaller than the cylinder is driven about an axis placed above the centerline of the cylinder.
The clearance between rotor and cylinder is small at the top but increases at the bottom.
The rotor carries vanes that move in and out as it rotates to maintain sealed spaces between the rotor and the cylinder wall. The vanes trap liquid or gas on the suction side and carry it to the discharge side, where contraction of the space expels it through the discharge line.The vanes may swing on pivots, or they may slide in slots in the rotor.
Diaphragm Pumps
Diaphragm pumps are also classified as positive displacement pumps because the diaphragm acts as a limited displacement piston. The pump will function when a diaphragm is forced into reciprocating motion by mechanical linkage, compressed air, or fluid from a pulsating, external source. The pump construction eliminates any contact between the liquid being pumped and the source of energy. This eliminates the possibility of leakage, which is important when handling toxic or very expensive liquids. Disadvantages include limited head and capacity range, and the necessity of check valves in the suction and discharge nozzles. An example of a diaphragm
pump is shown in Figure 20.
Diaphragm pumps are also classified as positive displacement pumps because the diaphragm acts as a limited displacement piston. The pump will function when a diaphragm is forced into reciprocating motion by mechanical linkage, compressed air, or fluid from a pulsating, external source. The pump construction eliminates any contact between the liquid being pumped and the source of energy. This eliminates the possibility of leakage, which is important when handling toxic or very expensive liquids. Disadvantages include limited head and capacity range, and the necessity of check valves in the suction and discharge nozzles. An example of a diaphragm
pump is shown in Figure 20.
Comments
Do not know much about the displacement pump. Because my degree dissertation was Finite Element Analysis the only part of mechanical engineering that I know is FEA (Finite Element Analysis). Therefore I can't comment on displacement pump. Just want to inform you that you have been added in my blogger Oil n Gas directory.Good luck in your future undertaking.
I am new in this all blogging thing. Yours is the first blog that i have read with so much of concentration. The information given by you, though its general in manner, is really something worth reading.
thanks for writing it...:-)
-Jack @ Inlet Filter
Diaphragm Pumps
classifiers